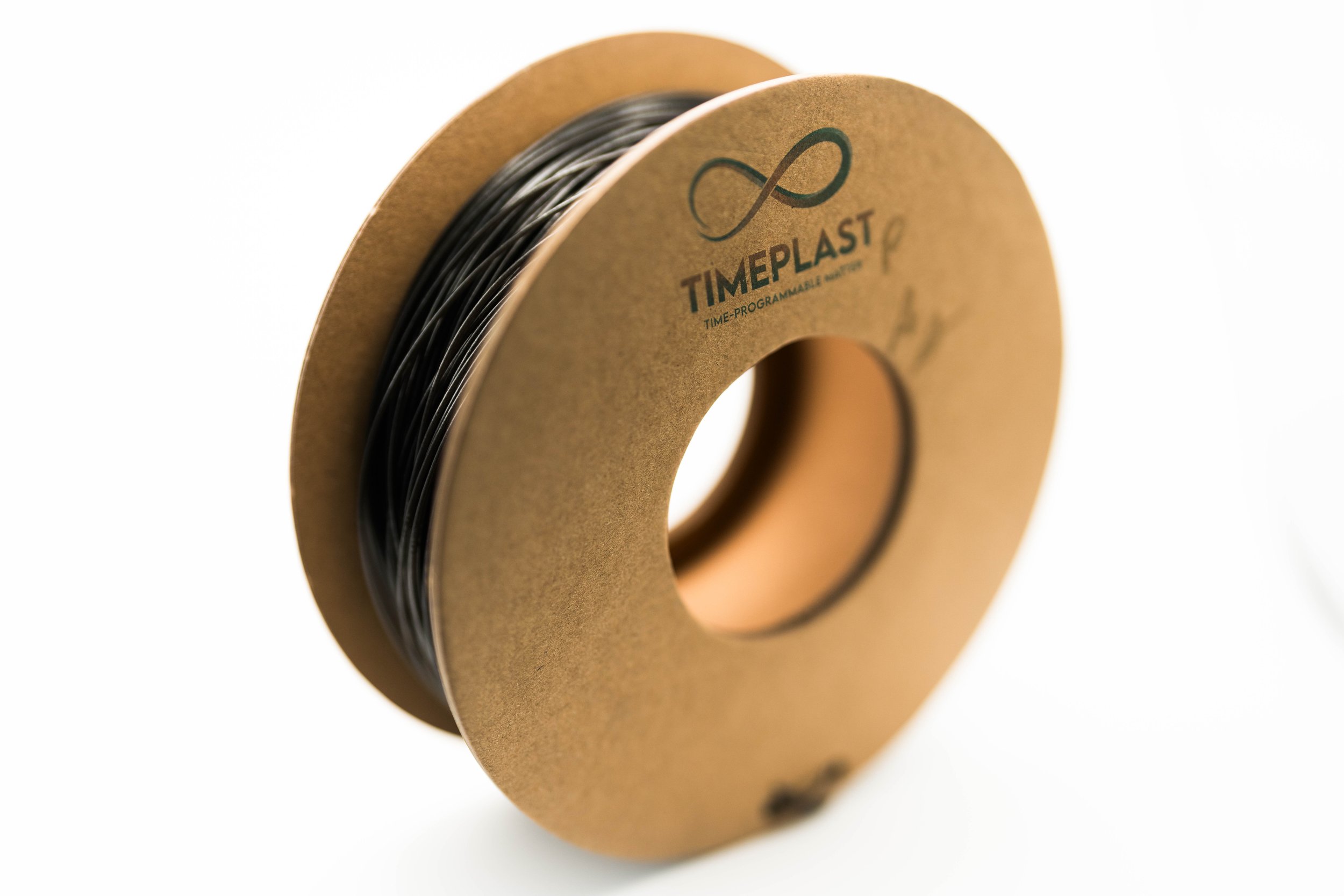
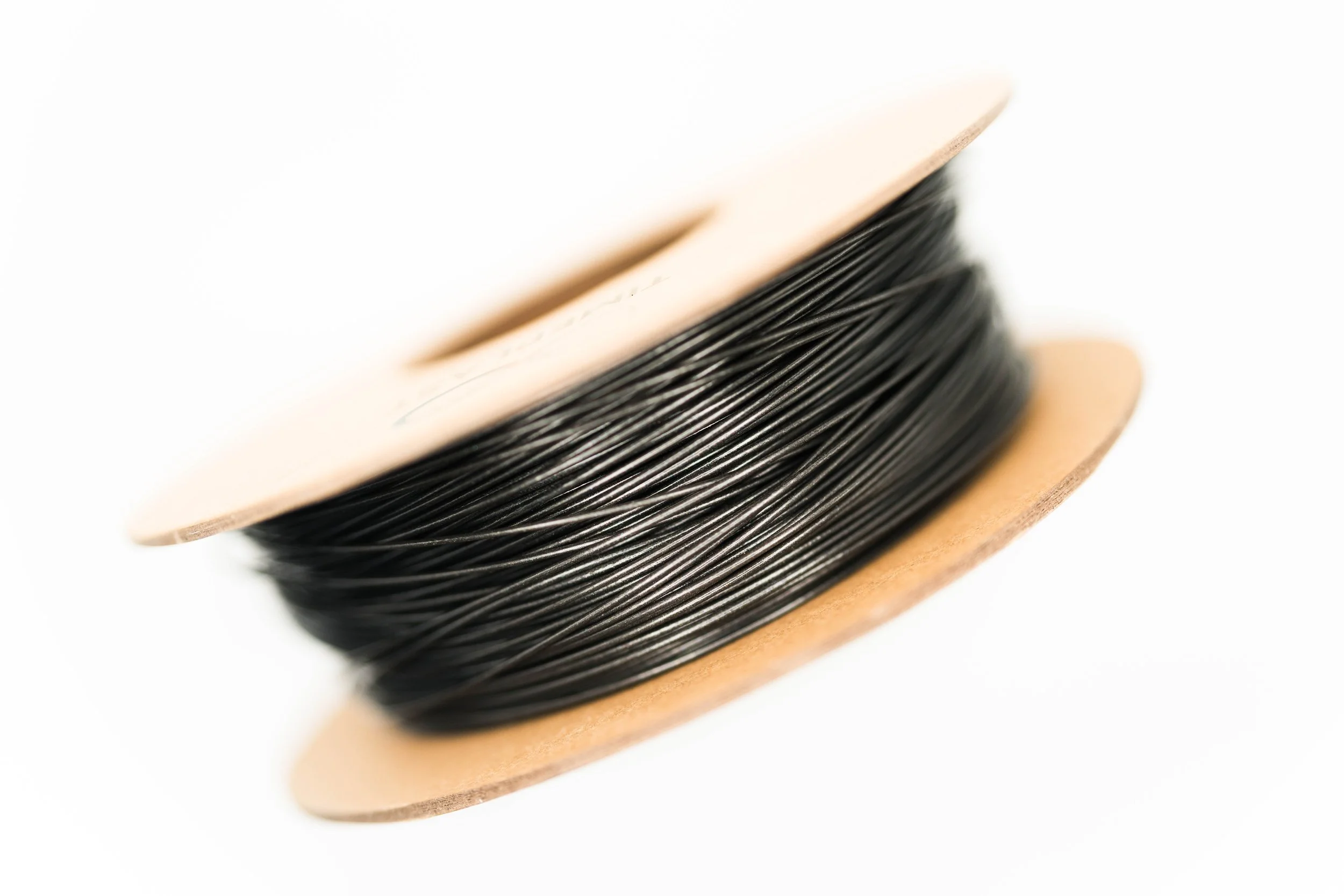
Passive
TimeMass Passive by Timeplast is a specialized 3D printing filament designed to be highly durable, stable, and resistant to external environmental factors. Unlike Time-Mass Active (which degrades over time) or TimeMass Fire (which is designed to burn), TimeMass Passive is engineered for long-term structural integrity, making it ideal for applications that require strength, longevity, and resistance to wear.
Key Features of TimeMass Passive:
🛠️ Highly Durable – Designed to last for extended periods without significant degradation.
🛡️ Resistant to Environmental Factors – Protects against moisture, UV exposure, and oxidation.
🔩 Structurally Strong – Can be used in applications requiring mechanical stability.
♻️ Sustainable & Non-Toxic – Developed with eco-friendly material science principles.
📏 Dimensional Stability – Maintains its form and function over time without warping or breaking down.
Why TimeMass Passive?
Timeplast designed TimeMass Passive as a material solution for industries and consumers needing durability without excessive waste. While many materials either degrade too quickly or persist indefinitely as pollutants, TimeMass Passive offers a balance—lasting as long as needed while remaining eco-conscious.
Need Ideas? Here You Go:
1. Long-Lasting Consumer Goods
Durable home decor and furniture components.
Weather-resistant outdoor accessories.
Sustainable, long-term-use kitchenware.
2. Industrial & Engineering Applications
Structural parts for 3D-printed machinery or tools.
Corrosion-resistant components for marine or aerospace applications.
Long-lasting prototypes for product development.
3. Infrastructure & Construction
3D-printed building materials that withstand the elements.
Durable interlocking tiles or modular structures.
Architectural elements requiring longevity.
4. Medical & Safety Equipment
Hygienic and long-lasting prosthetic components.
Non-degradable medical tools or diagnostic equipment.
Protective casings for sensitive instruments.
5. Automotive & Aerospace Applications
Heat and pressure-resistant vehicle components.
Protective covers for electronic and mechanical systems.
Long-term-use parts for sustainable transport solutions.Free U.S. Standard Shipping on orders of 5+ spools.
Custom colors & nutrient ratios for 5+ same-type spools’ orders
Made in the USA.
TimeMass Passive by Timeplast is a specialized 3D printing filament designed to be highly durable, stable, and resistant to external environmental factors. Unlike Time-Mass Active (which degrades over time) or TimeMass Fire (which is designed to burn), TimeMass Passive is engineered for long-term structural integrity, making it ideal for applications that require strength, longevity, and resistance to wear.
Key Features of TimeMass Passive:
🛠️ Highly Durable – Designed to last for extended periods without significant degradation.
🛡️ Resistant to Environmental Factors – Protects against moisture, UV exposure, and oxidation.
🔩 Structurally Strong – Can be used in applications requiring mechanical stability.
♻️ Sustainable & Non-Toxic – Developed with eco-friendly material science principles.
📏 Dimensional Stability – Maintains its form and function over time without warping or breaking down.
Why TimeMass Passive?
Timeplast designed TimeMass Passive as a material solution for industries and consumers needing durability without excessive waste. While many materials either degrade too quickly or persist indefinitely as pollutants, TimeMass Passive offers a balance—lasting as long as needed while remaining eco-conscious.
Need Ideas? Here You Go:
1. Long-Lasting Consumer Goods
Durable home decor and furniture components.
Weather-resistant outdoor accessories.
Sustainable, long-term-use kitchenware.
2. Industrial & Engineering Applications
Structural parts for 3D-printed machinery or tools.
Corrosion-resistant components for marine or aerospace applications.
Long-lasting prototypes for product development.
3. Infrastructure & Construction
3D-printed building materials that withstand the elements.
Durable interlocking tiles or modular structures.
Architectural elements requiring longevity.
4. Medical & Safety Equipment
Hygienic and long-lasting prosthetic components.
Non-degradable medical tools or diagnostic equipment.
Protective casings for sensitive instruments.
5. Automotive & Aerospace Applications
Heat and pressure-resistant vehicle components.
Protective covers for electronic and mechanical systems.
Long-term-use parts for sustainable transport solutions.Free U.S. Standard Shipping on orders of 5+ spools.
Custom colors & nutrient ratios for 5+ same-type spools’ orders
Made in the USA.
-
1. Introduction
These parameters are designed to help avoid printing issues; however, temperatures and speed timings can be adjusted based on your specific goals. For example, if you prefer a less rigid result, we recommend using a lower temperature. This is the printing guide for TimeMass Passive filament as tested on the Bambu Labs A1. This filament features extremely low moisture exchange, high structural stiffness, and requires higher thermal energy for optimal melt and flow. While these examples were printed with a 0.8 mm nozzle, TimeMass can be used with any nozzle size. Please check the manual for printing parameters with all the other nozzle sizes.Because TimeMass Passive releases minimal vapor but has high melt resistance and moderate elasticity, these profiles focus on thermal force management, mechanical flow stability, and precise extrusion tuning.
If the print is not being successful, please lower the nozzle temperature by 10°C and start over until an optimal print is achieved.2. Temperature Settings (All Nozzles)
2.a 0.2 mm Nozzle — Nozzle Temp: 235°C | Bed Temp: 70°C — High energy needed to soften the matrix
2.b 0.4 mm Nozzle — Nozzle Temp: 245°C | Bed Temp: 70°C — Better melt performance through standard nozzle size
2.c 0.6 mm Nozzle — Nozzle Temp: 250°C | Bed Temp: 70°C — Elevated flow demand for thick lines
2.d 0.8 mm Nozzle — Nozzle Temp: 255°C | Bed Temp: 70°C — Necessary thermal energy to prevent partial fusion at large diameterNote: Heatsink fans must remain consistent. Bed adhesion improves with light glue stick.
3. Cooling Settings (All Nozzles)
3.a No Cooling for First Layers: 2 — Less needed due to stiffer filament body
3.b Fan Minimum Speed: 20% at 50 seconds — Starts cooling sooner to shape rigid geometry
3.c Fan Maximum Speed: 25% — Supports layer definition without cracking
3.d Keep Fan Always On: ON — Essential for shaping passive structure
3.e Force Cooling Overhangs: ON — Encourages clean bridges for long spans
3.f Fan for Overhangs: 25–35% — Passive holds angles well, supports sharper fan controlNote: Timeplast Passive benefits from continuous airflow and structured cooling logic.
4. Max Volumetric Flow
4.a 0.2 mm Nozzle — Max Flow: 2 mm³/s — High-viscosity structure needs conservative flow
4.b 0.4 mm Nozzle — Max Flow: 5 mm³/s — Standard flow, safe and precise for rigid plastic
4.c 0.6 mm Nozzle — Max Flow: 9 mm³/s — Accommodates increased demand for high-mass lines
4.d 0.8 mm Nozzle — Max Flow: 13 mm³/s — Delivers clean, full-fused thick walls5. Retraction & Pressure Advance
5.a 0.2 mm Nozzle — Retraction: 1.0 mm @ 25 mm/s | Pressure Advance: 0.03
5.b 0.4 mm Nozzle — Retraction: 0.8 mm @ 20 mm/s | Pressure Advance: 0.04
5.c 0.6 mm Nozzle — Retraction: 0.6 mm @ 18 mm/s | Pressure Advance: 0.045
5.d 0.8 mm Nozzle — Retraction: 0.5 mm @ 15 mm/s | Pressure Advance: 0.05Note: Low moisture = less stringing, but retraction is still key for clean transitions.
6. Layer Height and Line Width
6.a 0.2 mm — Layer Height: 0.12 mm | Initial: 0.18 mm | Line Width: 0.25 mm
6.b 0.4 mm — Layer Height: 0.2 mm | Initial: 0.22 mm | Line Width: 0.42 mm
6.c 0.6 mm — Layer Height: 0.3 mm | Initial: 0.32 mm | Line Width: 0.6 mm
6.d 0.8 mm — Layer Height: 0.3 mm | Initial: 0.35 mm | Line Width: 0.8 mmNote: Clean lines support Timeplast Passive’s structural stiffness.
7. Wall, Shell & Infill Settings
7.a Wall Loops — 0.2 mm: 3 | 0.4 mm: 2–3 | 0.6 mm: 2 | 0.8 mm: 2
7.b Top/Bottom Shells — 0.2 mm & 0.4 mm: 4 | 0.6 mm & 0.8 mm: 3
7.c Top/Bottom Thickness — All: 1.2 mm (except 0.2 mm at 1 mm)
7.d Sparse Infill Density — 0.2 mm: 25% | 0.4 mm: 20–25% | 0.6 & 0.8 mm: 15–20%Note: Strong shells help support high stiffness and dimensional precision.
8. Speed & Acceleration
8.a Travel Speed — 0.2 mm: 120 mm/s | 0.4 mm: 140 mm/s | 0.6 mm: 150 mm/s | 0.8 mm: 160 mm/s
8.b Outer Wall Speed — 35 / 45 / 55 / 65 mm/s (increasing by nozzle size)
8.c Infill Speed — 70 / 100 / 120 / 130 mm/s
8.d Acceleration (Print) — 1200 / 1800 / 2200 / 2400 mm/s²
8.e Acceleration (Travel) — 3000 / 3500 / 4000 / 4500 mm/s²Note: Passive resists flex — high-speed print motion is safe and reliable.
9. Adhesion & Brims
9.a Skirt Loops: 1–2 — Clears dense first-line flow
9.b Brim Width: 5 mm — Secures stiffer corners to plate
9.c Brim Gap: 0.15 mm — Moderate release force to match rigidity10. Flush, Prime & G-code
10.a Prime Tower: Optional — Low moisture means less need for purging
10.b Start G-code:
nginx
CopyEdit
M900 K[PA] ; Pressure Advance M106 S0 ; Fan off G92 E0 G1 E15 F300 ; purge line G92 E0
Replace [PA] with the appropriate pressure advance value for your nozzle size.
11. Parameters That Stay Consistent Across All Nozzles
11.a Bed temperature: 70°C
11.b Seam logic and arc fitting: ON
11.c Retraction smoothing: Enabled
11.d Cooling delay: 2–3 layers
11.e Compatible with all standard Bambu Lab slicer toolsLet me know if you'd like this turned into a branded PDF or added to your existing documentation package.
You said:
can you please put (Dile que le ponga cursiva a los subtítulos y negrita a los títulos) thank you.
ChatGPT said:
Absolutely! Here's your fully formatted TimeMass Passive printing guide with:
Bold section titles
Italicized subtitles (e.g., numbered 2.a, 3.b, etc.)
Proper spacing for clarity
1. Introduction
This is the printing guide for TimeMass Passive filament as tested on the Bambu Labs A1. This filament features extremely low moisture exchange, high structural stiffness, and requires higher thermal energy for optimal melt and flow.Because TimeMass Passive releases minimal vapor but has high melt resistance and moderate elasticity, these profiles focus on thermal force management, mechanical flow stability, and precise extrusion tuning.
If the print is not being successful, please lower the nozzle temperature by 10°C and start over until an optimal print is achieved.2. Temperature Settings (All Nozzles)
2.a 0.2 mm Nozzle — Nozzle Temp: 235°C | Bed Temp: 70°C — High energy needed to soften the matrix
2.b 0.4 mm Nozzle — Nozzle Temp: 245°C | Bed Temp: 70°C — Better melt performance through standard nozzle size
2.c 0.6 mm Nozzle — Nozzle Temp: 250°C | Bed Temp: 70°C — Elevated flow demand for thick lines
2.d 0.8 mm Nozzle — Nozzle Temp: 255°C | Bed Temp: 70°C — Necessary thermal energy to prevent partial fusion at large diameterNote: Heatsink fans must remain consistent. Bed adhesion improves with light glue stick.
3. Cooling Settings (All Nozzles)
3.a No Cooling for First Layers: 2 — Less needed due to stiffer filament body
3.b Fan Minimum Speed: 20% at 50 seconds — Starts cooling sooner to shape rigid geometry
3.c Fan Maximum Speed: 25% — Supports layer definition without cracking
3.d Keep Fan Always On: ON — Essential for shaping passive structure
3.e Force Cooling Overhangs: ON — Encourages clean bridges for long spans
3.f Fan for Overhangs: 25–35% — Passive holds angles well, supports sharper fan controlNote: Timeplast Passive benefits from continuous airflow and structured cooling logic.
4. Max Volumetric Flow
4.a 0.2 mm Nozzle — Max Flow: 2 mm³/s — High-viscosity structure needs conservative flow
4.b 0.4 mm Nozzle — Max Flow: 5 mm³/s — Standard flow, safe and precise for rigid plastic
4.c 0.6 mm Nozzle — Max Flow: 9 mm³/s — Accommodates increased demand for high-mass lines
4.d 0.8 mm Nozzle — Max Flow: 13 mm³/s — Delivers clean, full-fused thick walls5. Retraction & Pressure Advance
5.a 0.2 mm Nozzle — Retraction: 1.0 mm @ 25 mm/s | Pressure Advance: 0.03
5.b 0.4 mm Nozzle — Retraction: 0.8 mm @ 20 mm/s | Pressure Advance: 0.04
5.c 0.6 mm Nozzle — Retraction: 0.6 mm @ 18 mm/s | Pressure Advance: 0.045
5.d 0.8 mm Nozzle — Retraction: 0.5 mm @ 15 mm/s | Pressure Advance: 0.05Note: Low moisture = less stringing, but retraction is still key for clean transitions.
6. Layer Height and Line Width
6.a 0.2 mm — Layer Height: 0.12 mm | Initial: 0.18 mm | Line Width: 0.25 mm
6.b 0.4 mm — Layer Height: 0.2 mm | Initial: 0.22 mm | Line Width: 0.42 mm
6.c 0.6 mm — Layer Height: 0.3 mm | Initial: 0.32 mm | Line Width: 0.6 mm
6.d 0.8 mm — Layer Height: 0.3 mm | Initial: 0.35 mm | Line Width: 0.8 mmNote: Clean lines support Timeplast Passive’s structural stiffness.
7. Wall, Shell & Infill Settings
7.a Wall Loops — 0.2 mm: 3 | 0.4 mm: 2–3 | 0.6 mm: 2 | 0.8 mm: 2
7.b Top/Bottom Shells — 0.2 mm & 0.4 mm: 4 | 0.6 mm & 0.8 mm: 3
7.c Top/Bottom Thickness — All: 1.2 mm (except 0.2 mm at 1 mm)
7.d Sparse Infill Density — 0.2 mm: 25% | 0.4 mm: 20–25% | 0.6 & 0.8 mm: 15–20%Note: Strong shells help support high stiffness and dimensional precision.
8. Speed & Acceleration
8.a Travel Speed — 0.2 mm: 120 mm/s | 0.4 mm: 140 mm/s | 0.6 mm: 150 mm/s | 0.8 mm: 160 mm/s
8.b Outer Wall Speed — 35 / 45 / 55 / 65 mm/s (increasing by nozzle size)
8.c Infill Speed — 70 / 100 / 120 / 130 mm/s
8.d Acceleration (Print) — 1200 / 1800 / 2200 / 2400 mm/s²
8.e Acceleration (Travel) — 3000 / 3500 / 4000 / 4500 mm/s²Note: Passive resists flex — high-speed print motion is safe and reliable.
9. Adhesion & Brims
9.a Skirt Loops: 1–2 — Clears dense first-line flow
9.b Brim Width: 5 mm — Secures stiffer corners to plate
9.c Brim Gap: 0.15 mm — Moderate release force to match rigidity10. Flush, Prime & G-code
10.a Prime Tower: Optional — Low moisture means less need for purging10.b Start G-code:
M900 K[PA] ; Pressure Advance M106 S0 ; Fan off G92 E0 G1 E15 F300 ; purge line G92 E0
Replace [PA] with the appropriate pressure advance value for your nozzle size.
11. Parameters That Stay Consistent Across All Nozzles
11.a Bed temperature: 70°C
11.b Seam logic and arc fitting: ON
11.c Retraction smoothing: Enabled
11.d Cooling delay: 2–3 layers
11.e Compatible with all standard Bambu Lab slicer tools
In all honesty, with TimeMass you won’t just print objects—you’ll print experiences. Think about it. By introducing a new programmable dimension, your designs don’t just sit there. They evolve. Shift. Light up. Soap up. Grow up. Phase out. Disappear and more. You’re actually building moments.
Precision? Built In.
Making a filament with Timeplast is not easy, not at all. We can’t use automated machines for example. Each spool is handcrafted, here in the U.S. and monitored by a human for over a 49-minute cycle per spool. That’s not mass production—that’s obsessive accuracy.
Specs That Actually Matter:
Diameter: 1.75mm
Mass: 0.77lb
Compatibility: Works with all major 3D printers. No drama.
True timed obsolescence
Use filaments with built-in "time codes" like Active, Delayed or Passive to make your prints transform, separate, or self-destruct on schedule. Whether it’s art, function, or straight-up sci-fi—if you can print it, you can make it move.
Water Molecular Disintegration – Print Today, Gone Tomorrow
Yes the words “Molecular Disintegration sounded like something that ChatGPT would say, but no, it’s the only way to explain how our materials dissolve in the presence of water down to a Carbon-to-carbon level. TimeMass breaks down at the molecular level when exposed to water. That’s not marketing—it’s chemistry. Smart materials that serve their purpose, then step aside. Clean, conscious, and built for next-gen applications.
By completing your order, you consent to receive email updates related to your purchase. We may also send you promotional offers, product news, and personalised recommendations. You can opt out at any time by clicking the "unsubscribe" link in any of our emails. Your information will be handled in accordance with our [Privacy Policy].