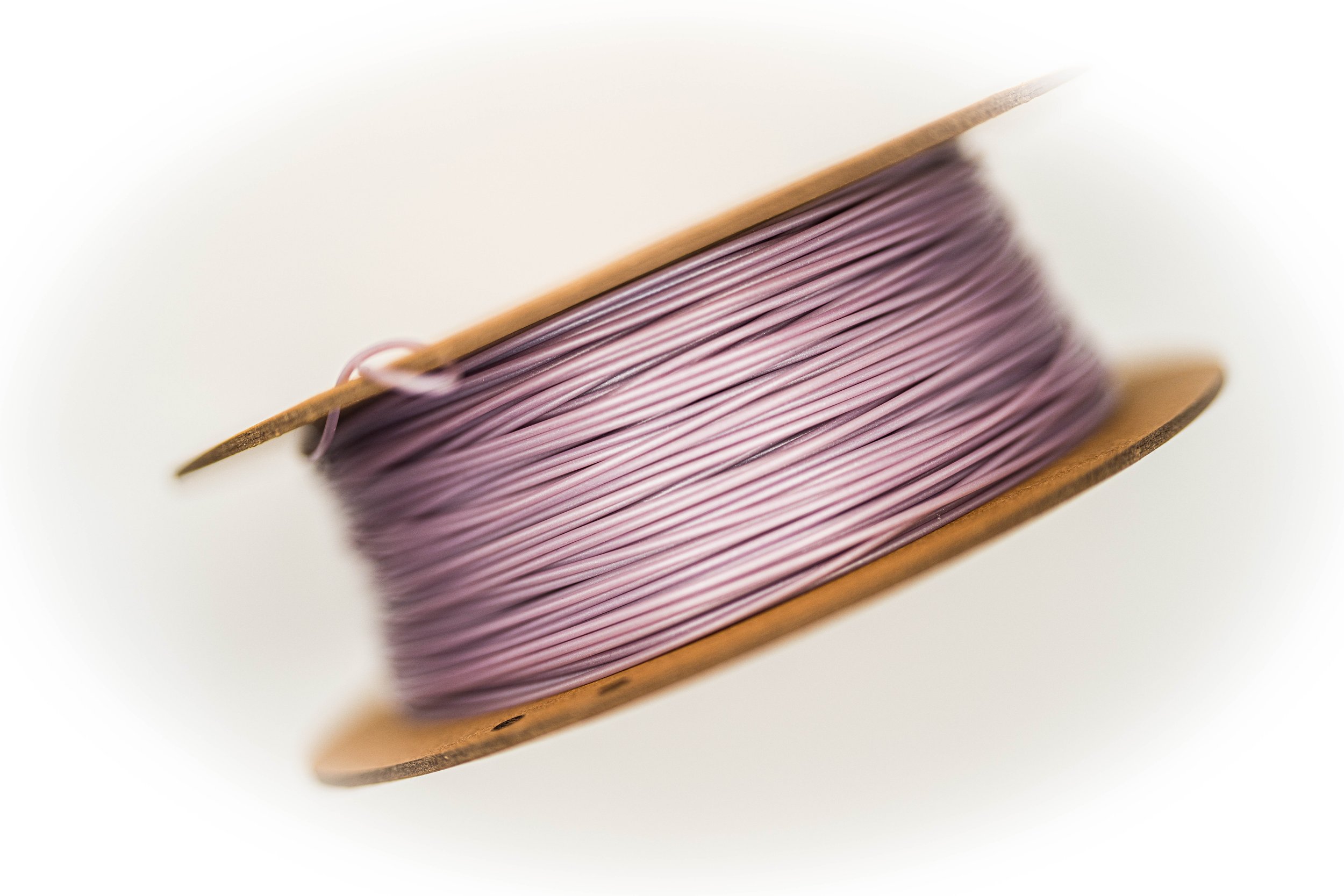
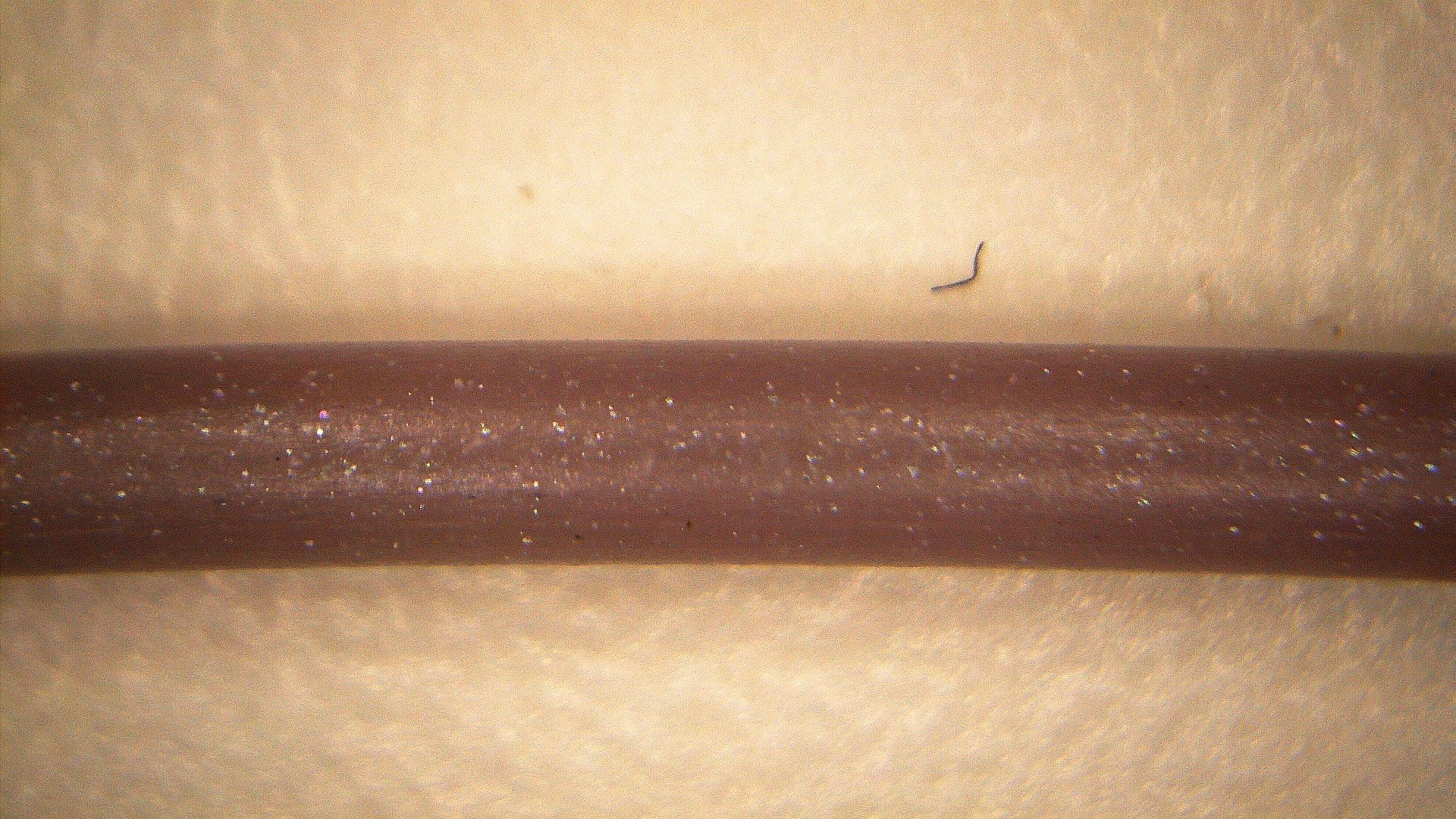
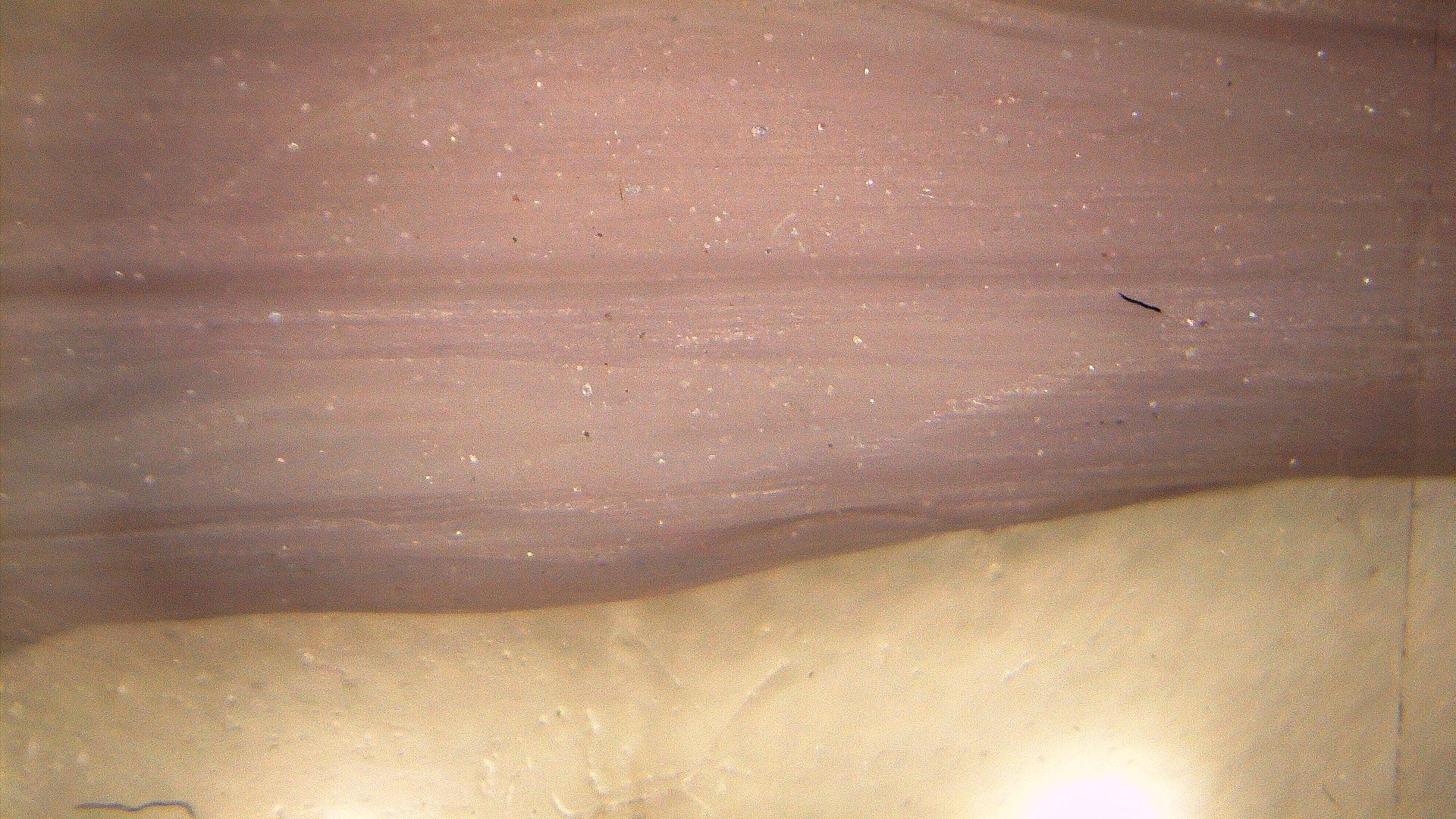

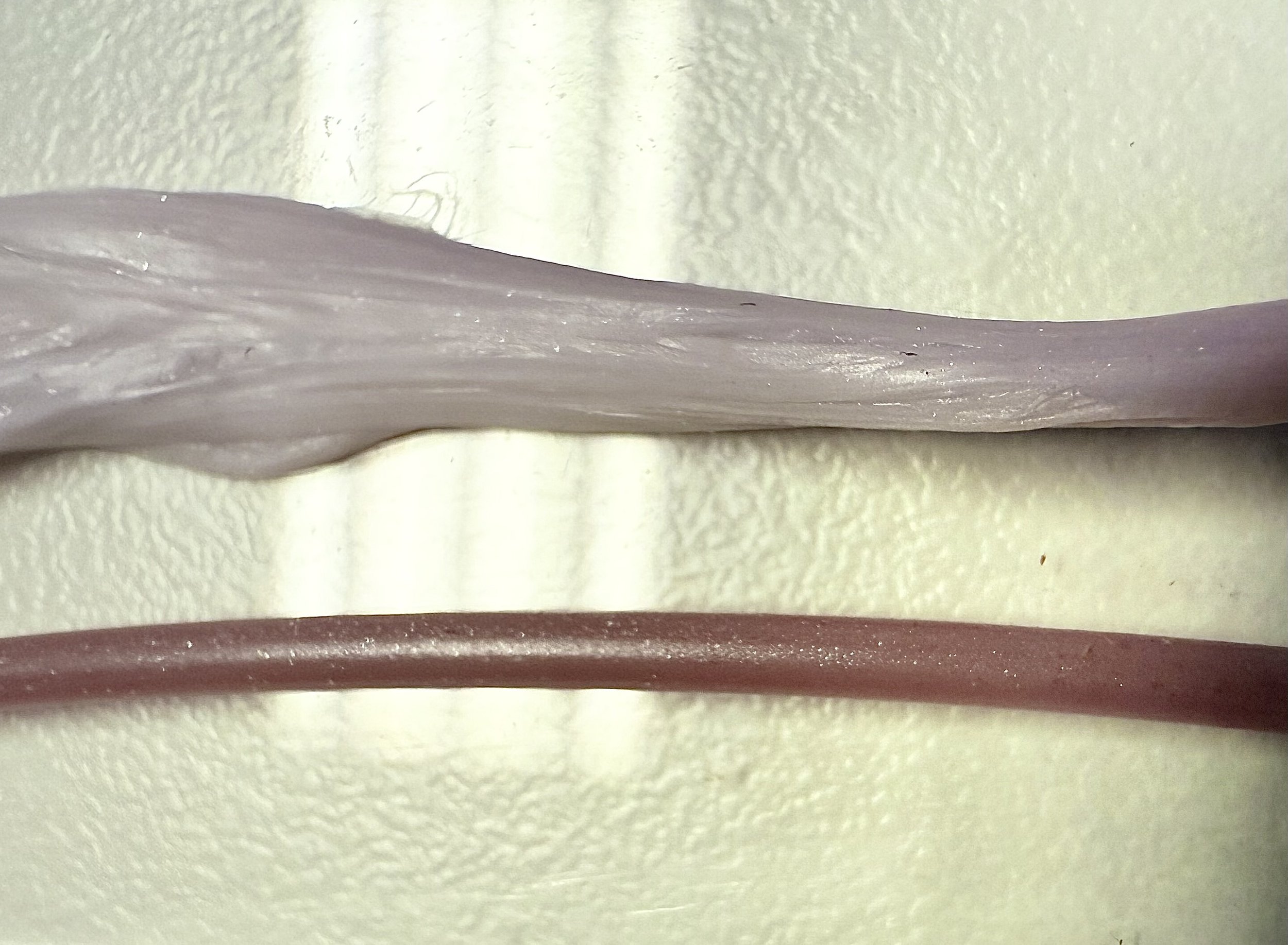
Fiber
TimeMass Fiber incorporates sacrificial polymer technology, which enables specific portions of the material to dissolve in a controlled manner. This feature is especially valuable in 3D printed soft fabrics, due to the small diameter of the remaining fibers. It is also used for advanced manufacturing and prototyping, as it allows for internal embedded supports, temporary reinforcements, or multi-material prints that transition over time.
After successfully printing an intricate fabric-like object using our TimeMass Fiber filament, you’ll need to submerge it in water for a period directly proportional to the softness you want to achieve.
For very soft fabrics, soak the object for 24 to 48 hours, depending on its thickness. The longer it remains submerged, the more of the sacrificial polymer will dissolve, leaving behind finer and more delicate fibers.
After the water treatment, it’s crucial to properly dry the material to finalize its structure. You can air-dry it in the sun or use a food dehydrator for a controlled process. The level of drying will directly impact the final texture—the more it dries, the firmer it becomes.
Mastering this filament involves experimentation, as balancing water exposure and drying time allows you to tailor the fabric’s softness to your specific needs and creative ideas.
How Sacrificial Polymer Technology Works in Time-Mass Fiber
Dual-Phase Composition – The filament consists of a durable, fiber-reinforced phase and a strategically embedded sacrificial polymer that weakens under water.
Post-Processing Activation – After printing, the sacrificial polymer can be removed through dissolution, thermal degradation, or mechanical peeling, leaving behind the intended final structure.
Self-Optimizing Material – The controlled removal of the sacrificial polymer can reduce weight, create internal channels, or improve flexibility in certain regions of the printed object.
Enhanced Printability – This technology ensures complex geometries print more reliably by integrating internal support structures that disappear when no longer needed.
Need Ideas? Here You Go:
Structural Components – Ideal for lightweight but strong or very soft parts in aerospace, automotive, and robotics. Depending on the sacrificial treatment.
Load-Bearing Prototypes – Useful for creating prototypes that need mechanical stress testing.
Sports Equipment & Protective Gear – Can be used in helmets, padding, and high-impact sports gear.
Medical Devices & Braces – Suitable for orthopedic supports and custom medical applications.
High-Performance Tooling – Can be used in jigs, fixtures, and manufacturing tools that require resilience.
Sustainable Consumer Products – Could be applied in eco-friendly furniture, accessories, or industrial design projects.
Free U.S. Standard Shipping on orders of 5+ spools.
Custom colors & nutrient ratios for 5+ same-type spools’ orders
Made in the USA.
TimeMass Fiber incorporates sacrificial polymer technology, which enables specific portions of the material to dissolve in a controlled manner. This feature is especially valuable in 3D printed soft fabrics, due to the small diameter of the remaining fibers. It is also used for advanced manufacturing and prototyping, as it allows for internal embedded supports, temporary reinforcements, or multi-material prints that transition over time.
After successfully printing an intricate fabric-like object using our TimeMass Fiber filament, you’ll need to submerge it in water for a period directly proportional to the softness you want to achieve.
For very soft fabrics, soak the object for 24 to 48 hours, depending on its thickness. The longer it remains submerged, the more of the sacrificial polymer will dissolve, leaving behind finer and more delicate fibers.
After the water treatment, it’s crucial to properly dry the material to finalize its structure. You can air-dry it in the sun or use a food dehydrator for a controlled process. The level of drying will directly impact the final texture—the more it dries, the firmer it becomes.
Mastering this filament involves experimentation, as balancing water exposure and drying time allows you to tailor the fabric’s softness to your specific needs and creative ideas.
How Sacrificial Polymer Technology Works in Time-Mass Fiber
Dual-Phase Composition – The filament consists of a durable, fiber-reinforced phase and a strategically embedded sacrificial polymer that weakens under water.
Post-Processing Activation – After printing, the sacrificial polymer can be removed through dissolution, thermal degradation, or mechanical peeling, leaving behind the intended final structure.
Self-Optimizing Material – The controlled removal of the sacrificial polymer can reduce weight, create internal channels, or improve flexibility in certain regions of the printed object.
Enhanced Printability – This technology ensures complex geometries print more reliably by integrating internal support structures that disappear when no longer needed.
Need Ideas? Here You Go:
Structural Components – Ideal for lightweight but strong or very soft parts in aerospace, automotive, and robotics. Depending on the sacrificial treatment.
Load-Bearing Prototypes – Useful for creating prototypes that need mechanical stress testing.
Sports Equipment & Protective Gear – Can be used in helmets, padding, and high-impact sports gear.
Medical Devices & Braces – Suitable for orthopedic supports and custom medical applications.
High-Performance Tooling – Can be used in jigs, fixtures, and manufacturing tools that require resilience.
Sustainable Consumer Products – Could be applied in eco-friendly furniture, accessories, or industrial design projects.
Free U.S. Standard Shipping on orders of 5+ spools.
Custom colors & nutrient ratios for 5+ same-type spools’ orders
Made in the USA.
-
These parameters are designed to help avoid printing issues; however, temperatures and speed timings can be adjusted based on your specific goals. For example, if you prefer a less rigid result, we recommend using a lower temperature. This is the printing reference for TimeMass Fiber filament, tested on the Bambu Labs A1 printer, and optimized for 0.2 mm, 0.4 mm, 0.6 mm, and 0.8 mm nozzles. TimeMass Fiber is more thermally sensitive and features a dual-phase structure, which emits more vapor during printing. It benefits from careful temperature ramping and reduced internal pressure. All settings are specifically optimized to reduce bubbling, fogging, and material instability. If the print fails, it is recommended to lower the nozzle temperature by 10°C and restart until optimal results are achieved. While these examples were printed with a 0.8 mm nozzle, TimeMass can be used with any nozzle size. Please check the manual for printing parameters with all the other nozzle sizes.
Temperature Settings vary by nozzle. For a 0.2 mm nozzle, set the nozzle temperature to 215°C and the bed to 60°C, optimizing for lower flow, finer bead, and less thermal stress. For 0.4 mm, use 225°C nozzle temperature and 60°C bed temperature to maintain melt uniformity for the encapsulated blend. The 0.6 mm nozzle works best at 230°C to ensure stable output for larger extrusion volumes, while the 0.8 mm nozzle should be set to 235°C, helping vapor escape from the larger filament volume without causing clogs. A textured PEI plate is required for adhesion—avoid smooth platesunless properly primed.
Cooling Settings should disable cooling for the first 3 layers to prevent fog formation under sensors. Set the fan minimum speed to 0% for the first 100 seconds to allow vapor to escape without becoming trapped. The maximum fan speed should be limited to 10–15%, preventing filament oval deformation. Keep the fan always off to avoid thermal shock and material stiffening mid-print. Do not force cooling on overhangs, and use only minimal airflow (10–15%)for structural overhangs.
Maximum Volumetric Flow varies per nozzle. For 0.2 mm, keep the flow at 1.5 mm³/s, which is sensitive to clogging due to low melt strength. For 0.4 mm, set it at 4 mm³/s, balancing for higher viscosity variance. The 0.6 mm should run at 6 mm³/s, avoiding pressure spikes and bubbles, and the 0.8 mm at 9 mm³/s, preventing vapor entrapment and melt lag. Ramming speed should be adjusted between 1–3 mm³/s depending on your purge tower strategy.
Retraction and Pressure Advance should be configured as follows: for a 0.2 mm nozzle, use a retraction distance of 0.7 mm at 20 mm/s speed, with a pressure advance of 0.04. For 0.4 mm, use 0.6 mm retraction, 18 mm/s speed, and 0.045 pressure advance. The 0.6 mm nozzle requires 0.5 mm retraction, 15 mm/s, and 0.05 advance, and the 0.8 mm nozzle performs best with 0.4 mm retraction, 15 mm/s, and 0.055 pressure advance. These values help manage off-gassing during slowdowns.
For Layer Height and Line Width, use 0.12 mm layer height, 0.18 mm initial layer, and 0.25 mm line width for the 0.2 mm nozzle. For 0.4 mm: 0.2 mm height, 0.22 mm initial, and 0.42 mm width. For 0.6 mm: 0.3 mm height, 0.32 mm initial, and 0.6 mm width. And for 0.8 mm: 0.3 mm height, 0.35 mm initial, and 0.8 mm width.
In terms of Wall, Shell, and Infill Settings, use 3 wall loops and 4 top/bottom shells for 0.2 mm and 0.4 mm nozzles, and 2 wall loops and 3 shells for 0.6 mm and 0.8 mm. Set top/bottom thickness to 1 mm for smaller nozzles and 1.2 mm for larger ones. Sparse infill density should be 30% for 0.2 mm, 25% for 0.4 mm, and 20–25% for 0.6 mm and 0.8 mm. These configurations support vapor containment inside internal zones.
Speed and Acceleration settings are as follows: For travel speed, use 100 mm/s (0.2 mm), 130 mm/s (0.4 mm), 140 mm/s (0.6 mm), and 150 mm/s (0.8 mm). Set outer wall speed to 30 mm/s, 35 mm/s, 45 mm/s, and 55 mm/s, respectively. Infill speed should be 50 mm/s to 100 mm/s, depending on nozzle size. For acceleration, print acceleration should range from 1000 mm/s² (0.2 mm) to 1800 mm/s² (0.8 mm), and travel acceleration from 2500 mm/s² to 4000 mm/s². These values are calibrated to reduce vibration and pressure surges.
For Adhesion and Brims, use 2 skirt loops to purge water vapor early. Set the brim width between 4 and 6 mm to stabilize softened edges during print start. A brim gap of 0.15 mm ensures easy release after printing.
Under Flush, Prime, and G-code, the use of a prime tower is recommended due to the heavy vapor released at the start of the print. Suggested start G-code is:
M900 K[PA] ; Pressure Advance M106 S0 ; Fan off G92 E0 G1 E15 F300 ; purge line G92 E0
Replace [PA] with the pressure advance value corresponding to your nozzle.
Lastly, parameters consistent across all nozzles include: Bed temperature of 60°C with a textured PEI bed, "Avoid crossing walls" set to ON, "Smart seam" ON, a cooling delay of 3 layers, and brim/skirt defaults remain functional. Always dry the filament before use, and it is recommended to print with the door open for optimal ventilation.
In all honesty, with TimeMass you won’t just print objects—you’ll print experiences. Think about it. By introducing a new programmable dimension, your designs don’t just sit there. They evolve. Shift. Light up. Soap up. Grow up. Phase out. Disappear and more. You’re actually building moments.
Precision? Built In.
Making a filament with Timeplast is not easy, not at all. We can’t use automated machines for example. Each spool is handcrafted, here in the U.S. and monitored by a human for over a 49-minute cycle per spool. That’s not mass production—that’s obsessive accuracy.
Specs That Actually Matter:
Diameter: 1.75mm
Mass: 0.77lb
Compatibility: Works with all major 3D printers. No drama.
True timed obsolescence
Use filaments with built-in "time codes" like Active, Delayed or Passive to make your prints transform, separate, or self-destruct on schedule. Whether it’s art, function, or straight-up sci-fi—if you can print it, you can make it move.
Water Molecular Disintegration – Print Today, Gone Tomorrow
Yes the words “Molecular Disintegration sounded like something that ChatGPT would say, but no, it’s the only way to explain how our materials dissolve in the presence of water down to a Carbon-to-carbon level. TimeMass breaks down at the molecular level when exposed to water. That’s not marketing—it’s chemistry. Smart materials that serve their purpose, then step aside. Clean, conscious, and built for next-gen applications.
By completing your order, you consent to receive email updates related to your purchase. We may also send you promotional offers, product news, and personalised recommendations. You can opt out at any time by clicking the "unsubscribe" link in any of our emails. Your information will be handled in accordance with our [Privacy Policy].